Products
3 Phase Transformer 25KVA | 63KVA | 100KVA | 250KVA
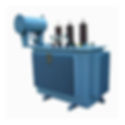


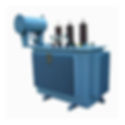
Specifications of Transformers
3 Phase Transformer
-
Oil Filling through Oil Impregnation procedure (Adapted generally for EHV transformer). It leads to enhanced life
-
Mineral Oil or Silicone Oil or as per requirement
-
Electrolytic Grade Copper winding
-
Low loss CRGO Silicon steel for core
-
Step lap construction & metered joints for core
-
Designed for extreme system supply variations and ambient temperature
-
Losses as per star rating (if required) as per BEE
-
Low Power Loss and Low Noise
SDT manufactures Power Transformers using advanced technology . Windings are made on automatic machines, the core & coil assembly is dried in vacuum drying oven of capacity 70 cubic meters. Transformers are rigorously tested at each stage of using modern testing equipments. We has already supplied many transformers which are successfully operation for more than 10 yrs.
​
Distribution transformers for industrial application is available in 3 phase version with primary voltages of up to 433V. The capacity range is up to 250 KVA. We manufacture single phase distribution transformers, three phase distribution transformers and industrial distribution transformers.
These single phase distribution transformers and three phase distribution transformers are available with 'Tap Changer' options as well as "Off Circuit Manually Operated" and "On Load Tap Changer" (OLTC) with AVR and RTCC panel. Prime quality, low loss, high permeability "Cold Rolled Grain Oriented" silicon steel is used for core to achieve low no load losses. These industrial distribution transformers have electrolytic copper with insulating paper multi covered round wires and strips are used for both the primary and secondary windings to achieve low load losses.
​
Copper foil winding technology is used for high current sections to achieve following advantages:
-
Sustaining short circuit forces without any distortion in low voltage and high current windings
-
Hot spot in LV windings regulated
-
No transposition, stray losses are minimal. Thus total copper losses are also further reduced
-
Total copper losses reduced vis-a-vis standard losses. Thus heat dissipating area also reduces
The high quality Standard setup by the company are appreciated by our customers in India and Abroad. Standards which are applied to development, manufacturing, installing and commissioning of power transformers for power stations, special purpose transformers for industry fields, reactors and accessories.
Our manufacturing facilities are located in Hyderabad. Power transformers up to 63 MVA 132 KV Class are regularly manufactured and supplied. SDT is equipped to manufacture transformers with a wide range of internationally recognized standards such as:
Unitised substation comprises of the following main components
Vacuum Circuit Breaker Panel in outdoor enclosure up to 250 KVA complete with CT / PT Relay & Instrument Chamber.
The outdoor circuit breaker panel is directly coupled to HT -Flange of the transformers with Copper Bus Bars.
The incoming of the HT panel is provided either with plug socket or cable box. Alternatively a Load Break Switch or Ring Main Unit (RMU)
Can also be coupled with the HT bushing of the transformer.
Outdoor transformers are manufactured up to 250KVA, DYII ONAN with off load tap changing switch and standard fittings as per IS, incoming HT panel and LT Flange to outgoing LT Panel. The Transformers can be either oil-immersed type Or Dry type with nomex insulation. With dry type transformers the total unit can be housed in single outdoor type enclosures in place of three separate Enclosures.
Setting high Standards as a consistent guarantee of the highest quality the company have achieved ISO 9001 certification for all its transformers. Regular internal and external quality audits ensure full and continues conformity with the international standards. The company's material and components suppliers are also required to satisfy these ISO standards Quality control is earned out a teach stage of production on a self-assessment basic. Each employee regards the next workstation as his customer and performs a series of quality checks before passing on a product down the line. The quality development department monitors all quality control documents and carries out its own additional inspection at strategic points in the production process. This system of checks and counter checks allows immediate action to be taken and modification to be made as required. All transformer tanks are tested before being released.to the customer. Testing includes leakage test and pressure test
Winding Connections
Tapping and phase leads are run in paper-covered conductors. the phase leads being separated from the tapping leads by adequate barriers. These tubes are rigidly brazed to ensure that required clearance from coil to tank is being maintained. L.V.Leads. larger in cross section, arc generally sufficient robust. but where necessary supports are provided.
Tank Construction
All tanks are made from mild sheet of adequate thickness with pressed steel fins cooling tube for heat dissipation. All tanks are checked by magna flux ultraviolet ray die penetrating system to ensure that there is absolutely no leakage from any part of the tank.
Quality Finish Through Use Of Shot
​
Blasting Technology
Tanks are shot blasted/ Grit blasted to remove mill and welding scale and then a primary coat is immediately applied to the exterior to eliminate rust formation. After priming all tanks receive a coat of high gloss paint, applied by spray. This ensures high coverage helping to combat corrosion in inaccessible places.
Insulation And Impregnation
The principal component of insulation is insulating Pre-compressed Press Board. The Components like rings, duct , dovetailed spacers, blocks etc are put under Compression along with the coil assembly for pre-shrinking . Providing additional insulation compensates the slight recovery
This reduces the probability of coils getting loose during operation an also minimizes the failure due to circuit forces.
In Order to prevent deformation under short-circuit forces, solid insulator end locks and rings are used. Windings are compressed under top and bottom clamping embers with the help of tie rods. The axial end thrust under fault Condition is minimized by the suitable balance to the ampere-turns over the length of windings. In case of bigger transformers, the HV taping leads are taken out from two positions to balance the short circuit forces in a much better way. At SDT each and every component used in transformer undergoes a series of stringent checks and controls at each stage of manufacturing and it is ensured that strict technical & qualitative specifications are adhered to Utmost care is taken while manufacturing and assembling every component of a transformer.
The main process line of a transformer is:
Core : The core is constructed from lamination of imported Cold Rolled Grain Oriented (CRGO), low loss electrical steel. The cores are assembled in jigs prior to tapping and clamping in a manner that reduces vibration and inherent varnish, which is both oil and heat resistant and complete core is connected to the clamps to ensure that it is effectively earthen.
The Core legs are surely bound with heavy duty insulating tape and the yokes are firmly clamped between folded steel channels. Tops & bottoms clamps are secured to each other by means of tie rods which serve the dual purpose of securing the windings in the place and of transferring the load form the bottom to the top clamps when the core and windings are lifted. This prevents any tensile stress hoeing setup in the core legs which could adversely affect the iron losses.
Winding : Windings, or Coils are designed to meet three fundamental requirements, mechanical, Thermal & electrical. They are cylindrical in sharwand are wound concentrically. Both H.V.& L.V. windings are wounds with adequate brazing and securing tapes in order to achieve a strong and self-supporting structure. Inter layer ducts arc provided to ensure low temperature gradient between winding and oil and thus any hot spot temperature is kept to minimum. This insures that the rate of insulation deterioration is minimized and high life expectancy is achieved.
Features
-
Rating: 4* & 5*
-
Voltage Class: 433v
-
Frequency: 50 / 60 Hz or as per requirement
-
Tap Types: Off Circuit Tap Switch / On Load Tap Changer
-
Temperature Rise: 40o C
-
Vector Group: Dyn11
-
Cooling: ONAN